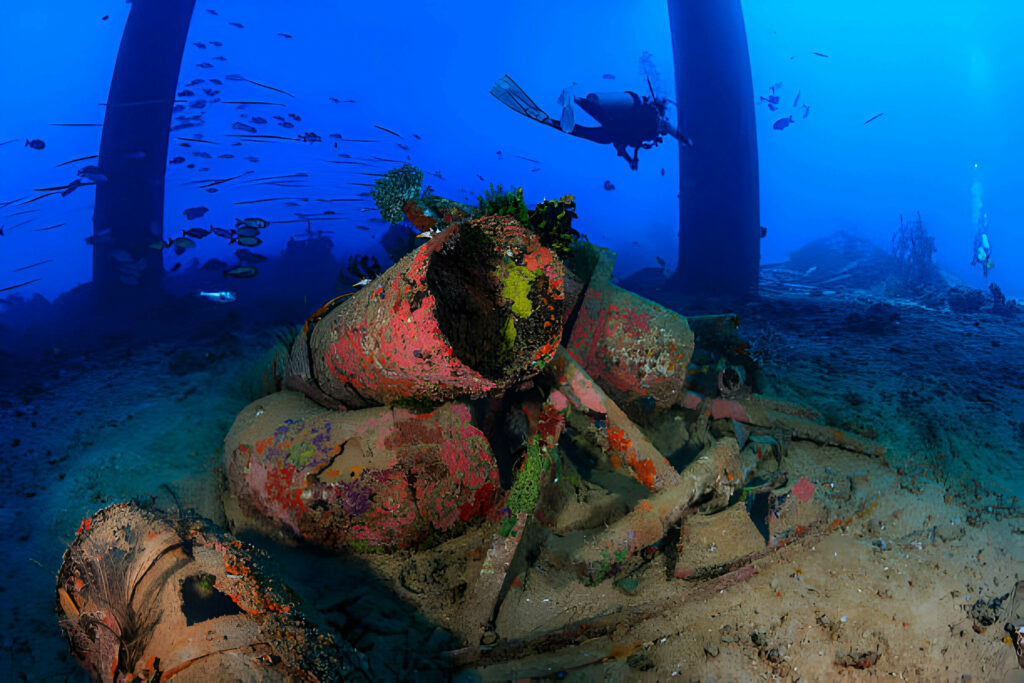
The Channel Tunnel, often referred to as the Eurotunnel or the Chunnel, is a true engineering marvel that stands as one of the greatest achievements in subsea construction. Connecting the United Kingdom and France under the English Channel, the tunnel stretches for 50.45 kilometers (31.3 miles), with 37.9 kilometers (23.5 miles) beneath the seabed. It is the longest underwater tunnel in the world and remains a critical piece of infrastructure for both passenger and freight transport.
The construction of the Channel Tunnel required unprecedented technological innovation, collaboration across national borders, and the overcoming of significant engineering and logistical challenges. It also presented lessons that continue to shape subsea engineering, tunnel design, and international construction projects. This article takes a deep dive into the engineering triumphs of the Channel Tunnel and examines the lessons learned during its construction.
The Channel Tunnel Project: A Brief Overview
The Channel Tunnel project, initiated in the late 1980s and completed in 1994, was a collaborative effort between the UK and France. The project was ambitious, not only in terms of its technical challenges but also due to the scale of its economic, political, and environmental scope.
The tunnel was designed primarily to facilitate rail transport, allowing high-speed trains (such as the Eurostar) to travel between London and Paris in under 3 hours. It also serves as an important route for freight, providing a faster, more efficient alternative to sea and road transport. The tunnel runs beneath the English Channel, one of the busiest and most challenging bodies of water to work in, with its unpredictable tides, strong currents, and highly varied geology.
The Engineering Challenges of the Channel Tunnel
Constructing a tunnel beneath the sea requires solving a myriad of engineering challenges, including pressure management, groundwater control, and tunneling through complex geological layers. The Channel Tunnel project faced unique obstacles that demanded innovative solutions:
1. Geological Complexity
The geology beneath the English Channel posed a major challenge. Engineers had to work through soft clay, sandstone, and chalk while also navigating the presence of water and other subterranean features. The chalk marl was especially problematic because it would become unstable when wet.
- Solution: To deal with this, engineers used a combination of TBMs (Tunnel Boring Machines) and traditional drilling methods. The TBMs were custom-designed to bore through both solid rock and more friable, wet soil, and they were equipped with advanced mucking systems to remove debris. The chalk marl was also injected with stabilizing agents to ensure it would not collapse during construction.
2. Water Ingress and Groundwater Management
One of the most significant concerns when tunneling underwater is the pressure exerted by water and the risk of water ingress. The Channel Tunnel was designed to operate below the seabed, where the pressure would be immense, especially at the tunnel’s lowest points.
- Solution: To manage the water pressure, engineers implemented high-strength concrete for the tunnel’s lining, which could withstand the immense forces from water pressure. The tunnel’s design also incorporated multiple layers of waterproofing, including bituminous seals and waterproof membranes, to prevent water from entering. Additionally, the tunnel was built with a drainage system that diverted water from any potential leaks and kept the tunnel dry.
3. Safety in Confined, High-pressure Environments
Safety during the tunneling process was a top priority due to the confined nature of working underground and underwater. The Channel Tunnel’s length, combined with the significant depth beneath the seabed, meant that the workforce was exposed to high-pressure environments.
- Solution: To ensure worker safety, a saturation diving system was used for deep work in the underwater section. Divers were kept at high pressure inside diving bells or chambers to avoid decompression sickness. Furthermore, the tunnel’s final design included sophisticated ventilation systems and emergency escape routes to protect the workers once the tunnel was in operation.
Technological Innovations: The Tools of the Trade
The successful construction of the Channel Tunnel relied heavily on the development and application of innovative technologies. Several breakthroughs in engineering and tunneling techniques were used to make the project feasible:
1. Tunnel Boring Machines (TBMs)
The Channel Tunnel’s TBMs were key to excavating the tunnel through challenging geological formations. The project required 11 different TBMs, each with specific features tailored to the diverse ground conditions. These machines were capable of digging through both solid rock and softer layers, while simultaneously lining the tunnel with concrete segments.
- Innovation: The multi-functionality of these TBMs was a significant innovation. They not only excavated but also laid the tunnel’s inner lining, reducing the time and complexity of the construction process. The use of continuous shielding in the TBMs ensured the tunnel remained structurally sound as it was being dug.
2. Waterproofing Systems
As mentioned, the tunnel’s waterproofing was critical due to the high water pressure beneath the Channel. The Channel Tunnel used several advanced techniques to ensure the tunnel’s integrity:
- Flexible waterproof membranes: These membranes were designed to expand and contract, accommodating movement without cracking, thus preventing water ingress.
- Bituminous seals: A durable, waterproof material was applied along the tunnel’s lining to prevent leaks.
- Polymer-based grouts: These were injected into small cracks and gaps during construction, further enhancing the tunnel’s water-tightness.
3. Ventilation and Air Quality Systems
Given the confined space of the tunnel, a reliable ventilation system was critical for providing fresh air to the workers during construction, as well as for the safety of passengers once the tunnel opened.
- Innovation: The tunnel’s ventilation system uses fan rooms and air shafts at regular intervals along the tunnel. The air in the tunnel is pumped out to maintain air quality and ensure there is no build-up of carbon dioxide. The system also helps to keep the tunnel at a comfortable temperature for both workers and passengers.
Key Lessons from the Channel Tunnel
The construction of the Channel Tunnel was not without its difficulties and setbacks, but the successful completion of the project provided several valuable lessons for subsea and tunneling engineering:
1. The Importance of Geotechnical Surveys
A comprehensive understanding of the ground and seabed conditions before starting a major construction project is critical. The Channel Tunnel was constructed through a variety of geological formations, and the more detailed the geotechnical surveys, the better prepared engineers were for unexpected geological conditions. The extensive geological studies that were conducted helped minimize the risk of unforeseen obstacles during construction.
2. Collaborative International Efforts Are Key
The Channel Tunnel required significant international cooperation between the UK and France, as well as numerous contractors, suppliers, and engineers from across the globe. The collaboration fostered innovation and allowed the project to overcome various challenges efficiently. This international teamwork is a lesson for large infrastructure projects involving multiple stakeholders.
3. Managing Water Ingress in Subsea Construction
The Channel Tunnel project underscored the importance of ensuring the waterproofing of subsea tunnels. Engineers must take into account the long-term challenges of water ingress and develop systems that ensure safety, reduce maintenance needs, and maintain structural integrity over time.
4. Advanced Technology and Automation
The use of advanced technology, such as Tunnel Boring Machines and real-time data collection, greatly enhanced the efficiency and safety of the project. The lesson here is the importance of investing in cutting-edge technology to increase productivity, minimize risks, and improve construction timelines, especially when dealing with extreme conditions like subsea environments.
5. Safety and Worker Protection Are Paramount
Ensuring the safety of workers in high-pressure, confined, and hazardous environments is essential. The Channel Tunnel project demonstrated that detailed safety protocols, saturation diving systems, and emergency escape plans are crucial for the successful completion of such risky endeavors.
Conclusion: A Legacy of Innovation and Excellence
The Channel Tunnel stands as a testament to human ingenuity and the ability to overcome extreme challenges. It not only remains a symbol of international cooperation but also offers critical lessons in subsea engineering, tunneling, and infrastructure development. The innovative techniques, safety measures, and technologies developed for the tunnel have become foundational to subsea projects around the world.
As the world continues to push the boundaries of engineering, the lessons learned from the Channel Tunnel will undoubtedly continue to inform future endeavors in subsea infrastructure, making them safer, more efficient, and more sustainable.